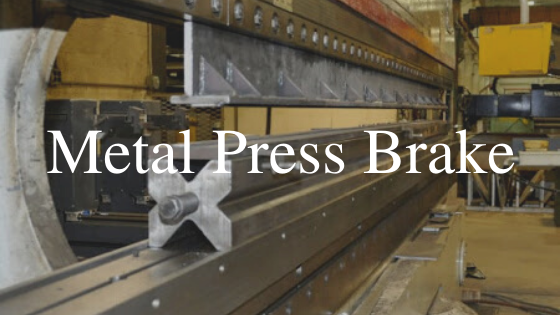
Metal Bending Basics
Metal has been an integral part of human culture for over 10,000 years. Ancient cultures used locally discovered metals such as copper, lead, iron and gold to create decorative items and tools. Some cultures even developed techniques to create stronger alloys over the centuries. Metals that could be bent into different shapes were very undesirable during ancient times. Much more effort was dedicated to creating materials that could withstand stress and pressure. It was not until much later when some of the first bending processes were developed.
Anvils And Hammers:
One of the oldest techniques used to bend metal involves a heat source, an anvil and a hammer. The metal is heated over an incredibly hot fire until it becomes malleable. A metalworker or blacksmith then uses a stable base like an anvil and a hammer to shape the metal. Each strike of the hammer deforms the piece until the correct curve or bend is achieved. This sometimes required a very long time since the piece would have to be repeatedly heated and pounded over the course of many hours. This is how some helmets, shields and decorative items were created.
Manual Brakes:
The first manual brakes started to appear before the industrial age. The first brakes were large machines that could not be easily moved. They were used in factories in order to create parts for construction, commercial exteriors and industrial equipment. They became very important in the emerging maritime industry. The brakes were not easy to use and required strength and skill. Manual brakes are still in use today although they are much lighter and often have features that make bends very accurate.
Modern Brakes:
A modern press brake was first developed during World War II in order to help streamline production of equipment and vehicles for the military. Most modern brakes use hydraulic, pneumatic or motorized systems to move a ram downwards into a sheet of metal. The ram pushes the metal into a specially cut die that allows a precision bend to be made. Press brakes are now so accurate and easy to use that a single person can produce dozens of pieces in a very short period of time.
Cutting-Edge Systems:
The latest press brakes, such as the Shenchong metal press brake, are connected to computers that use special software, live optical sensors and other tracking devices in order to remove the chance of an operator error or malfunction that could destroy a piece of metal. The computers also use pressure sensors to detect the performance of a ram when working with unusual metals. Computerization of advanced brakes is making it possible to produce increasingly sophisticated pieces for residential and industrial use.
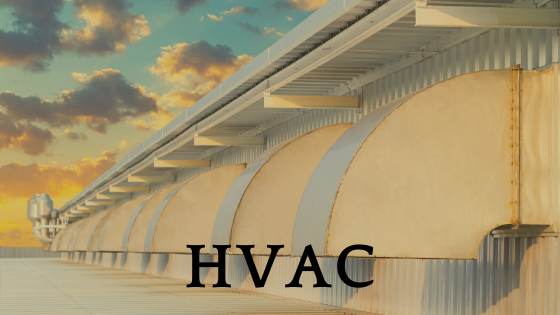
Barns HVAC
You May Also Like
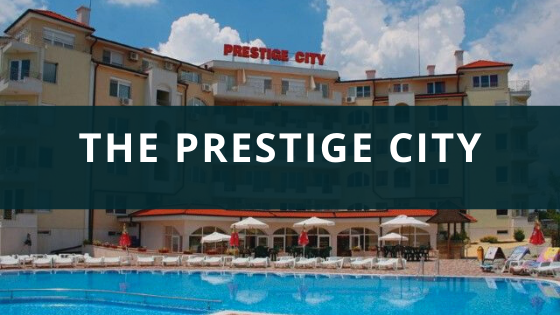
Bangalore Luxury Real Estate
September 27, 2021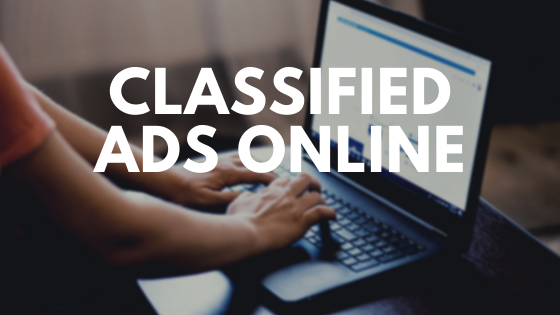
Tips for a successful classified ad campaign
January 22, 2021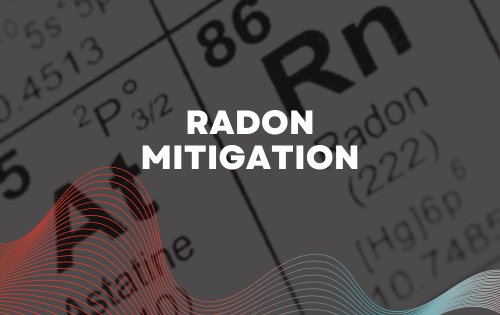